
Galvanized H-shaped steel
Can be processed, need specific combination
Keywords: Galvanized H-shaped steel
Series:
Product Details
Galvanized H-beams, also known as galvanized H-shaped steel beams, are structural steel components that have been coated with a layer of zinc to enhance their resistance to corrosion. These beams are widely used in construction and various industrial applications due to their strength, durability, and aesthetic appeal. This article will explore the properties, manufacturing process, advantages, and applications of galvanized H-beams, providing a comprehensive understanding of their significance in modern engineering.
Properties of Galvanized H-Beams
Galvanized H-beams possess several key properties that make them an ideal choice for construction and structural applications. Firstly, their H-shape provides excellent load-bearing capacity, allowing them to support heavy loads while maintaining stability. The wide flanges of the H-beam help distribute weight evenly, reducing the risk of structural failure.
Secondly, the galvanization process adds a layer of zinc to the surface of the steel, providing exceptional corrosion resistance. This is particularly important in environments exposed to moisture, chemicals, and other corrosive elements. The zinc coating acts as a sacrificial barrier, protecting the underlying steel from rust and degradation.
Additionally, galvanized H-beams are known for their lightweight nature compared to traditional steel beams. This characteristic facilitates easier handling and installation, reducing labor costs and construction time. The combination of strength, corrosion resistance, and lightweight design makes galvanized H-beams a popular choice in various construction projects.
Manufacturing Process
The manufacturing process of galvanized H-beams involves several stages, ensuring high-quality products that meet industry standards. The first step is the production of the H-beam itself, which is typically made from hot-rolled steel. The steel is shaped into an H-profile through a series of rolling processes, creating the characteristic shape with two parallel flanges connected by a vertical web.
Once the H-beam is formed, it undergoes the galvanization process. This involves cleaning the steel surface to remove any contaminants, such as oil, rust, or scale. After cleaning, the beam is immersed in a molten bath of zinc at a temperature of approximately 450°C. The zinc adheres to the steel surface, forming a metallurgical bond that ensures long-lasting protection against corrosion.
After galvanization, the H-beams are inspected for quality and compliance with relevant standards. This may include testing for thickness of the zinc coating, adhesion, and overall structural integrity. Once approved, the galvanized H-beams are cut to size and prepared for delivery to construction sites or industrial applications.
Advantages of Galvanized H-Beams
The use of galvanized H-beams offers numerous advantages over traditional steel beams. One of the most significant benefits is their enhanced durability. The zinc coating protects against rust and corrosion, extending the lifespan of the beam and reducing the need for maintenance and repairs. This is particularly advantageous in harsh environments where exposure to moisture and chemicals is common.
Another advantage is the aesthetic appeal of galvanized H-beams. The shiny, metallic finish of the zinc coating adds a modern touch to structures, making them visually appealing. This is especially important in architectural applications where design and aesthetics play a crucial role.
Galvanized H-beams are also environmentally friendly. The galvanization process is sustainable, and the long lifespan of these beams reduces the need for frequent replacements, minimizing waste. Additionally, at the end of their life cycle, galvanized steel can be recycled, contributing to a circular economy.
Applications of Galvanized H-Beams
Galvanized H-beams find applications in a wide range of industries, including construction, manufacturing, and infrastructure. In the construction sector, they are commonly used in the framing of buildings, bridges, and industrial structures. Their strength and durability make them suitable for supporting heavy loads, ensuring the safety and stability of the overall structure.
In manufacturing, galvanized H-beams are utilized in the production of machinery and equipment. Their corrosion resistance makes them ideal for components exposed to harsh conditions, such as in chemical plants or food processing facilities.
Infrastructure projects also benefit from the use of galvanized H-beams. They are often employed in the construction of highways, railways, and other transportation systems. The ability to withstand environmental challenges while maintaining structural integrity makes them a reliable choice for these critical applications.
Conclusion
In conclusion, galvanized H-beams are an essential component in modern construction and industrial applications. Their unique properties, including strength, corrosion resistance, and lightweight design, make them a preferred choice for engineers and architects alike. The manufacturing process ensures high-quality products that meet stringent standards, while the numerous advantages, such as durability and aesthetic appeal, further enhance their value.
As the demand for sustainable and resilient building materials continues to grow, galvanized H-beams are poised to play a significant role in shaping the future of construction and infrastructure. Their versatility and reliability make them a key player in the ongoing evolution of engineering practices, paving the way for innovative and enduring structures.
Previous Article
Next Article
Previous Article
Next Article
Series Related Products
FAQ
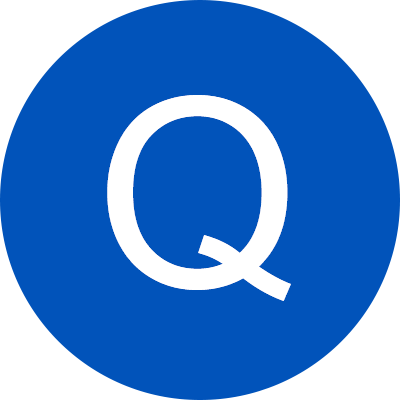
Can I go to your factory to visit?
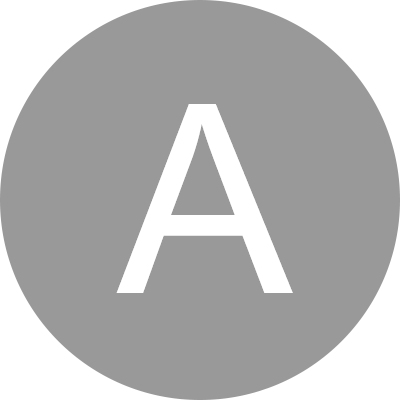
Of course, we welcome customers from all over the world to visit our factory.
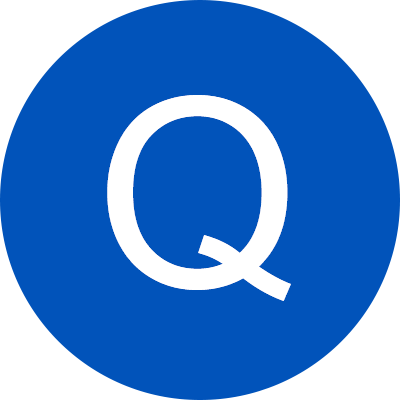
Do you accept customized orders?
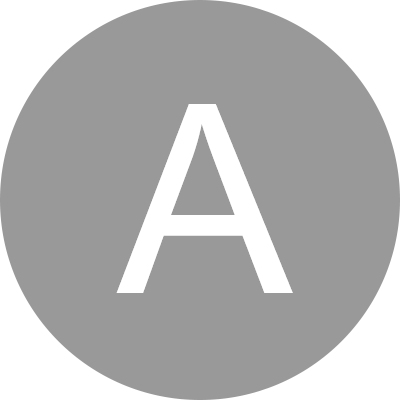
Yes,just tell us your requirements
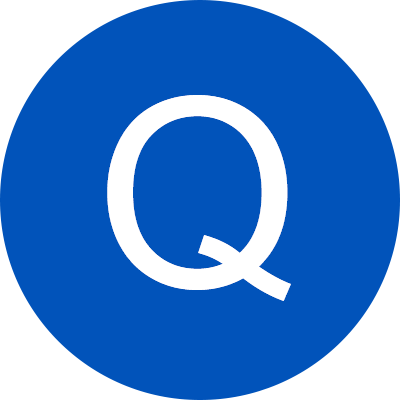
What's your delivery time?
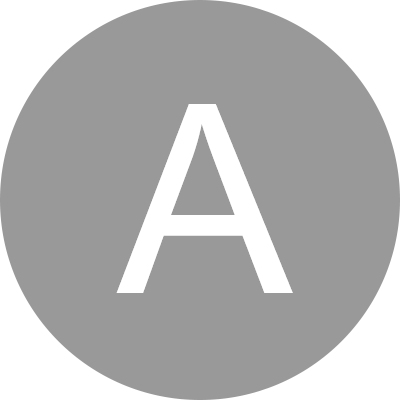
Within 7 days fastest,7-15days
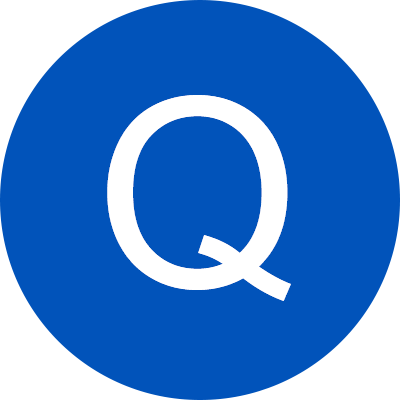
How about MOQ?
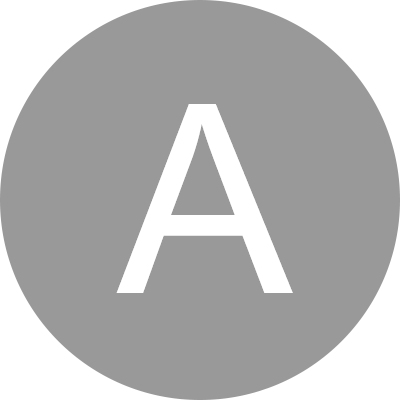
The minimum order quantity is 1 ton, which can be customized according to customer requirements. Please feel free to leave us message if you have any question about us and our products.